Quick Summary: Why RFID for Inventory Management? The Case for RFID Tags in a Modern Business In today’s data-driven world, relying on manual inventory tracking can lead to blind spots and labor-intensive processes. RFID (Radio Frequency Identification) technology offers a streamlined alternative, giving enterprise organizations real-time insights into their assets, tools, and equipment. By adopting RFID tags for inventory, you can drastically reduce errors, minimize loss, and enable proactive decision-making across the entire operation. RFID Tags for Seamless Inventory Management! AssetPulse RFID Solutions…
Category: RFID Solutions
Learn how RFID solutions enhance asset tracking, improve accuracy, and streamline operations. Explore the benefits and applications of RFID technology in various industries.
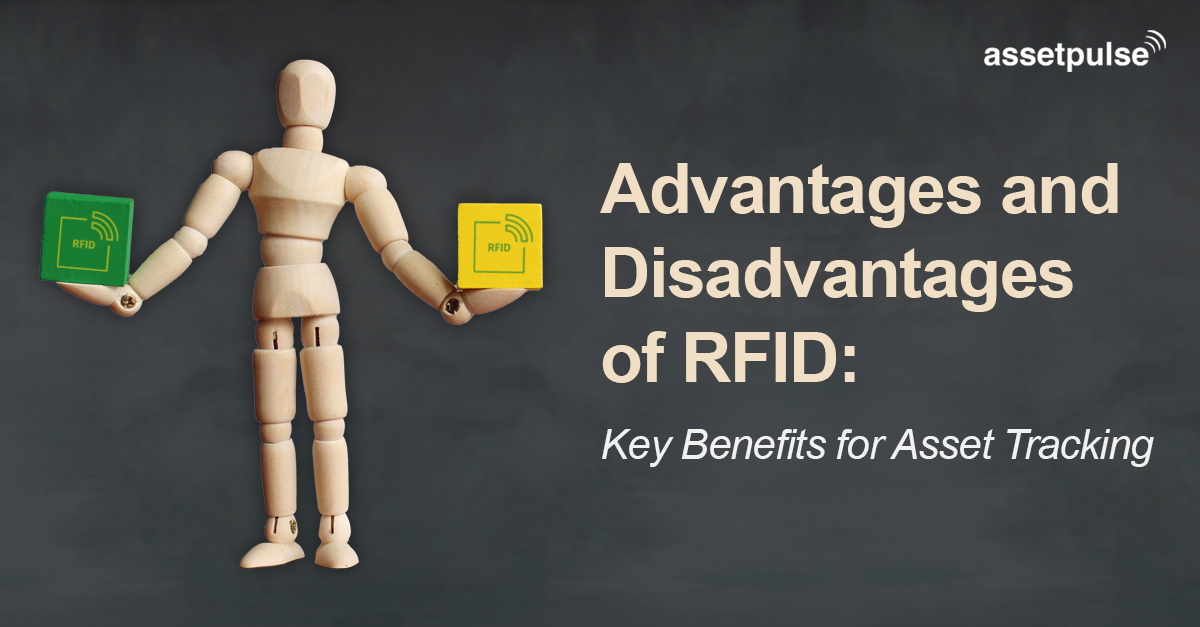
Advantages and Disadvantages of RFID: Key Benefits for Asset Tracking
If you’re evaluating RFID to replace or supplement barcodes, you’re likely asking: “What are the advantages and disadvantages of RFID?” and “Why is RFID important?” Radio Frequency Identification (RFID) has been around for decades, but recent innovation shave made it more reliable and cost-effective. Today, RFID tags and scanners help businesses in manufacturing, healthcare, IT, Labs, and many other sectors. Below, we’ll explore the key benefits (advantages) of RFID, as well as some drawbacks you should consider before deploying an RFID tracking system. Want to…
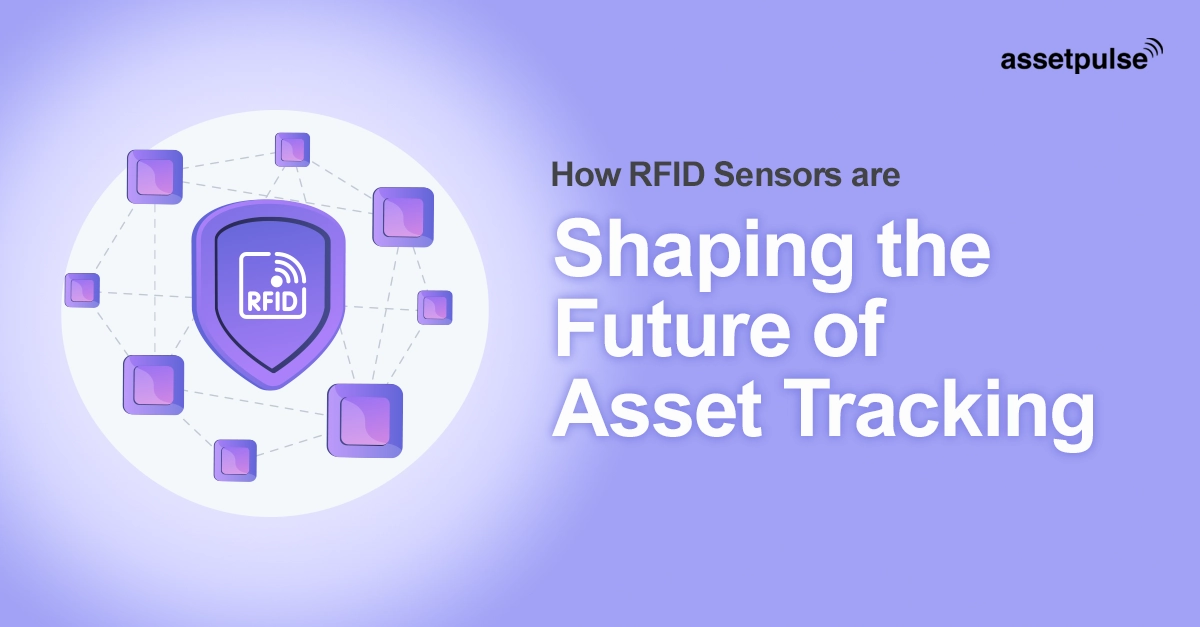
How RFID Sensors are Shaping the Future of Asset Tracking
In today’s fast-paced world, the ability to efficiently track and manage assets is paramount across industries. From supply chain management to inventory control, RFID sensors have emerged as a game-changer, transforming how businesses operate. But what exactly are RFID sensors, and how do they work? Let’s dive in. Boost Efficiency with RFID Sensors Gain Real-Time Visibility and Accuracy with AssetPulse RFID Solutions Get Free Consultation Understanding RFID Sensors RFID, also known as Radio Frequency Identification, utilizes radio waves to wirelessly…
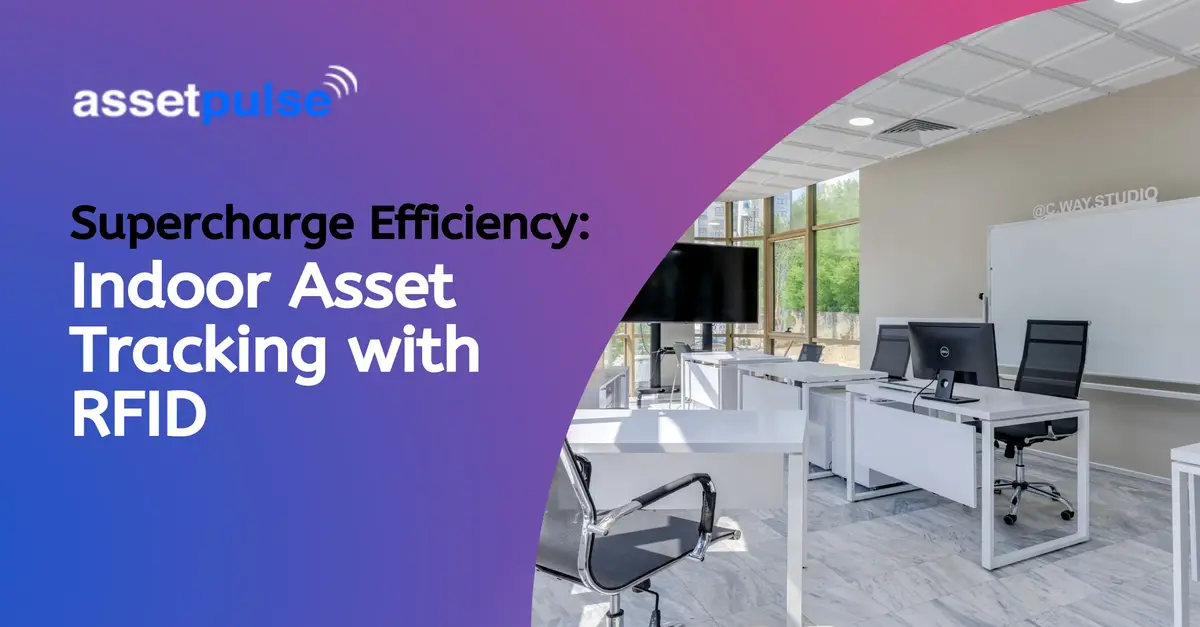
Supercharge Efficiency: Indoor Asset Tracking with RFID
Imagine a world where misplaced tools in factories, missing lab equipment in laboratories, or misplaced laptops in offices are a thing of the past. Indoor asset tracking makes this a reality, offering real-time visibility and streamlined management of physical assets within a building. This technology empowers businesses to optimize asset utilization and unlock significant efficiency gains. This blog dives deep into how RFID revolutionizes indoor asset tracking. Why Indoor Asset Tracking Matters In today’s competitive environment, maximizing the use of your…
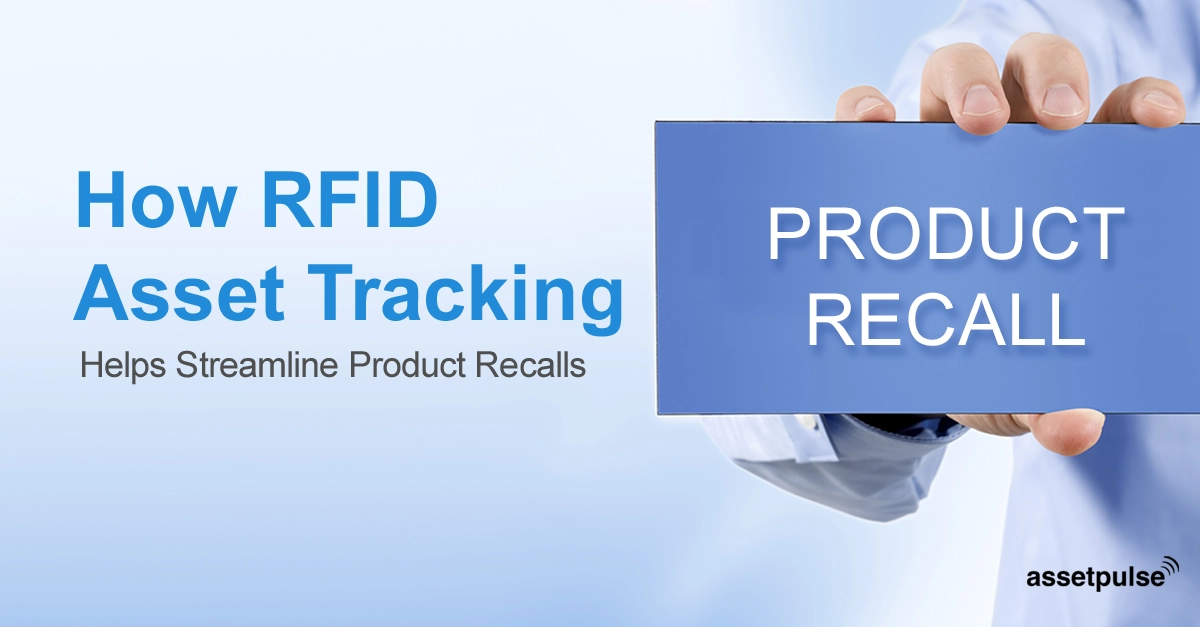
How RFID Asset Tracking Helps Streamline Product Recalls
Product recalls are a nightmare for any manufacturer. They can damage your reputation, cost you millions or billions based on the product, and expose you to legal risks. In this blog post, we will explain what product recalls are, why they happen, what challenges they pose, and how RFID asset tracking can help you handle them more effectively. What is a Product Recall A product recall is a request from a manufacturer to return, exchange, or replace a product after…