Ensuring robust personnel tracking in cleanrooms is vital for maintaining operational safety and regulatory compliance. In today’s high-security environments, where maintaining accurate logs of who enters and exits and enforcing strict access guidelines are critical. RFID technology is emerging as a transformative tool. Modern cleanrooms demand more than just physical barriers. They require a dynamic system that monitors personnel movement and even tracks the use of essential protective gear. With RFID integrated into your cleanroom access management strategy, you can…
Category: Asset Tracking Software
Discover how asset tracking software enhances efficiency and accuracy in managing your valuable assets. Explore benefits, features, and solutions tailored for streamlined operations.
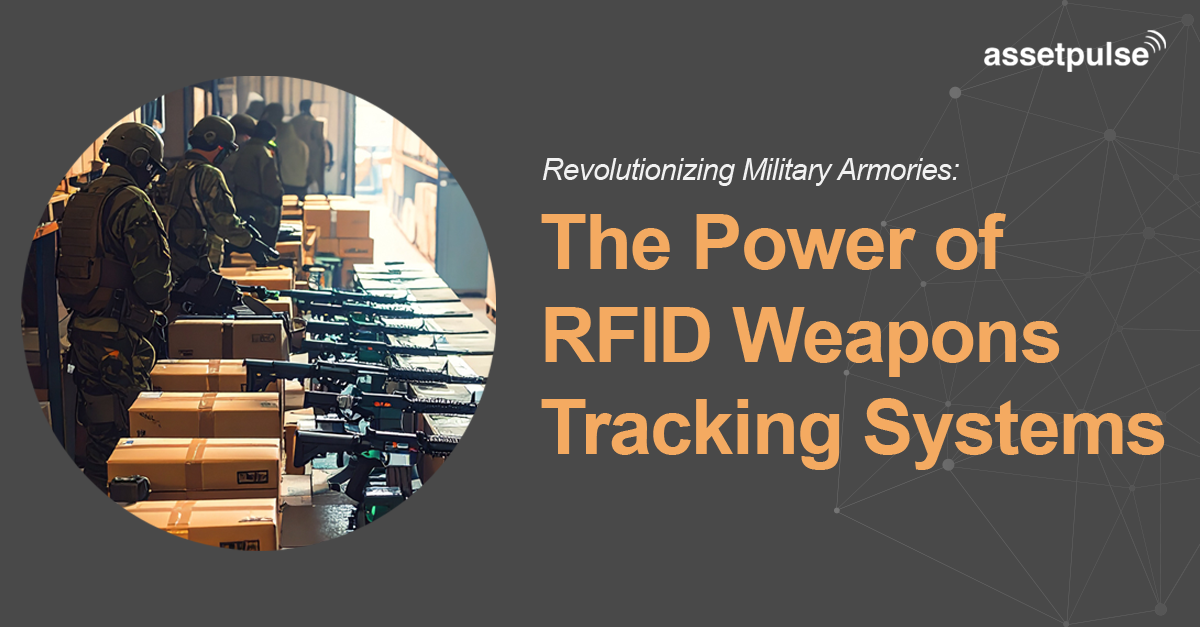
Revolutionizing Military Armories: The Power of RFID Weapons Tracking Systems
Military bases worldwide—whether operated by the Army, Navy, Air Force, or Marines—depend on secure armories to manage and safeguard their weapons. Each day, as soldiers are issued M16s, hand pistols, and automatic weapons for their shifts, these assets must be returned and meticulously accounted for at the end of each cycle. Traditionally, this responsibility has rested with armorers who manually count every weapon, verify serial numbers, and log data by hand. This labor-intensive process, repeated three times a day across…
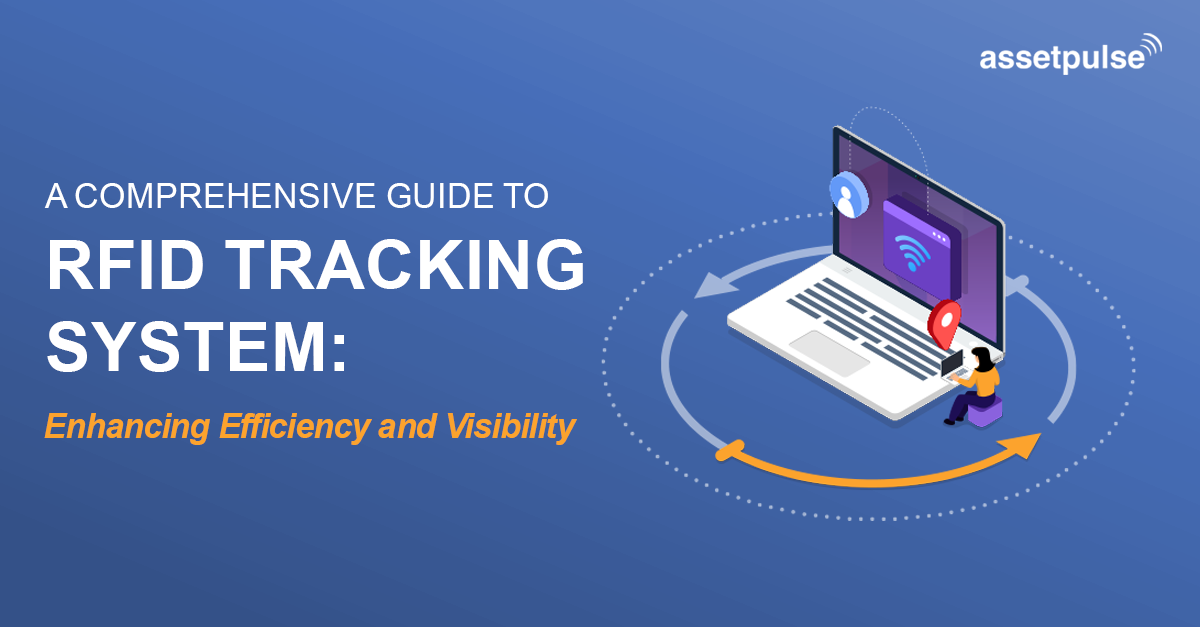
The Comprehensive Guide to RFID Tracking System: Enhancing Efficiency and Visibility
In today’s dynamic business environment, having precise control over your assets isn’t just a luxury—it’s a necessity. For enterprises looking to streamline their operations, an RFID tracking system offers a proven solution. This guide will walk you through what RFID tracking system is all about, its key components, and show you how this technology can transform your operations by boosting accuracy, cutting costs, and improving overall efficiency. Want to know how RFID streamlines your operations? Discover the power of AssetPulse…
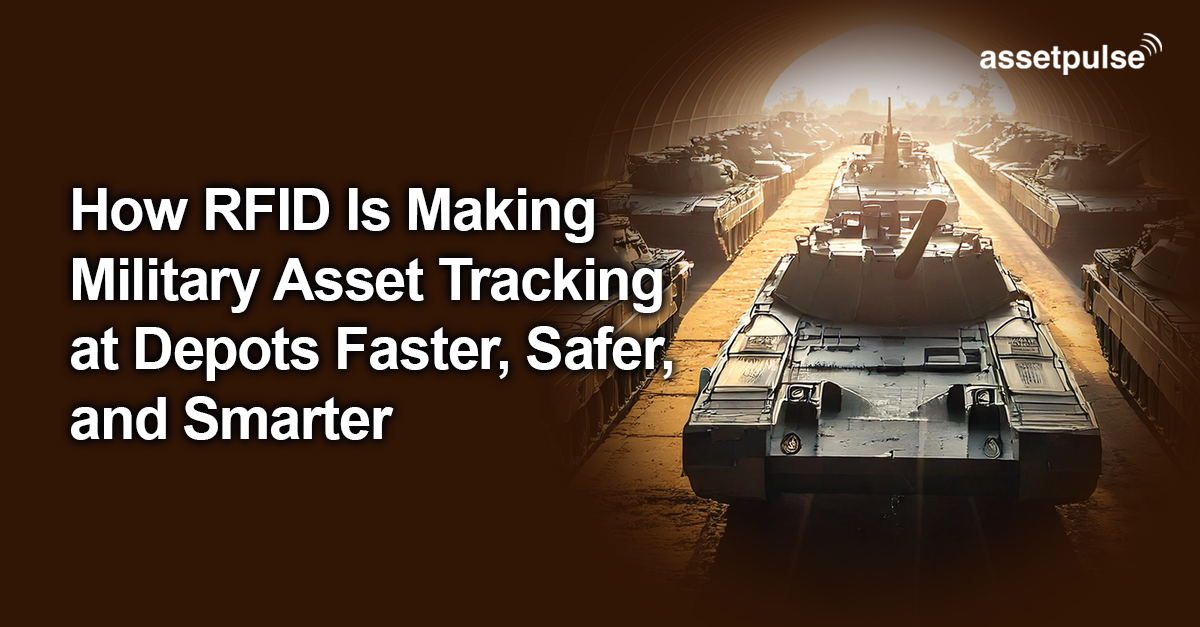
How RFID Is Making Military Asset Tracking at Depots Faster, Safer, and Smarter
Managing a massive army depot—packed with thousands of tanks, trucks, and weapons—is a huge challenge. Old-school tracking methods, like writing down serial numbers by hand or using paper logs, are extremely inefficient, messy, and error prone. These outdated asset tracking systems can’t keep up with the speed of modern warfare. That’s where RFID (Radio Frequency Identification) comes in handy. This post breaks down how RFID fixes these problems and why it’s a game-changer for modern military facilities. Upgrade your depot with RFID…
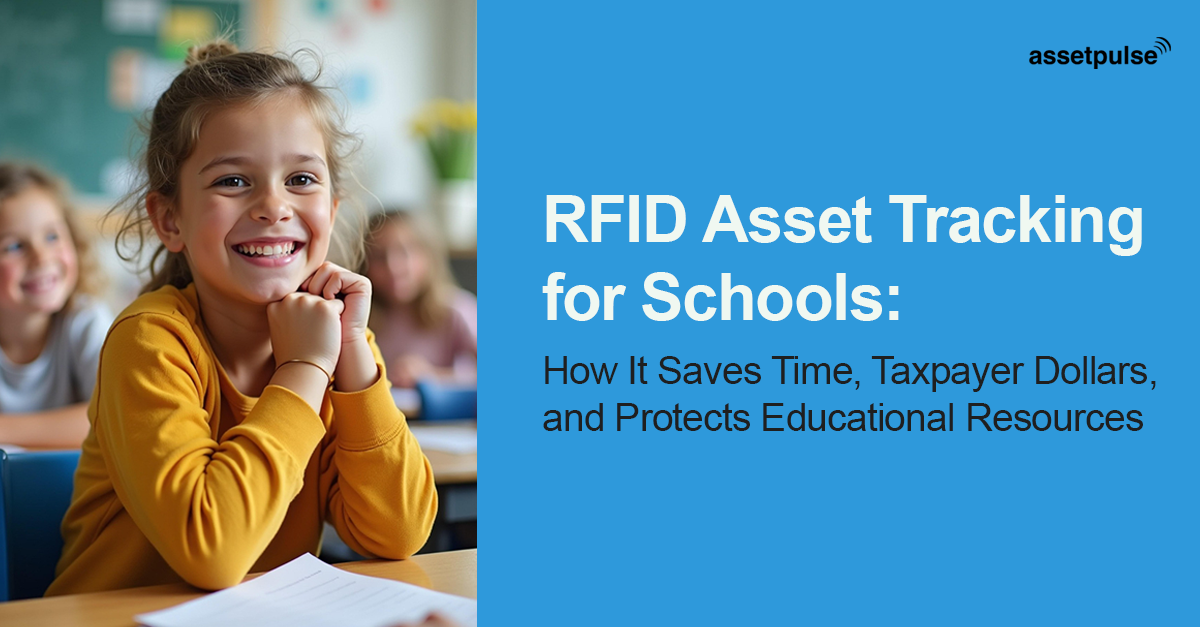
RFID Asset Tracking for Schools: How It Saves Time, Taxpayer Dollars, and Protects Educational Resources
Public schools across the United States are the backbone of our education system, funded by taxpayer dollars and state budgets. With this funding comes the responsibility to manage educational assets—like desks, chairs, tables, filing cabinets, and library racks—efficiently and transparently. However, manually tracking these assets can be a daunting, time-consuming task. This is where RFID asset tracking come in handy, a game-changer for school asset management that’s transforming how schools safeguard their resources. In this blog post, we’ll explore how RFID asset tracking…