Organizations have to apply well-defined GMP practices in cleanrooms and labs in order to maintain particulate and pathogen free environments. There are formal requirements and guidelines for food, drug, medical device and cosmetics manufacturing where sanitized conditions are maintained. There are several cleaning standards including the ISO14644 and the Federal Standard 209E standards. Since they are operated under strict guidelines, they are subject to several cleaning methodologies. Some of the common SOPs (standard operating procedures) include chemical wipe downs, autoclaving…
Category: Oil and Gas
Discover how asset tracking solutions improve efficiency, safety, and compliance in the oil and gas industry. Learn best practices for managing critical assets.
Oil and Gas
Continue Reading
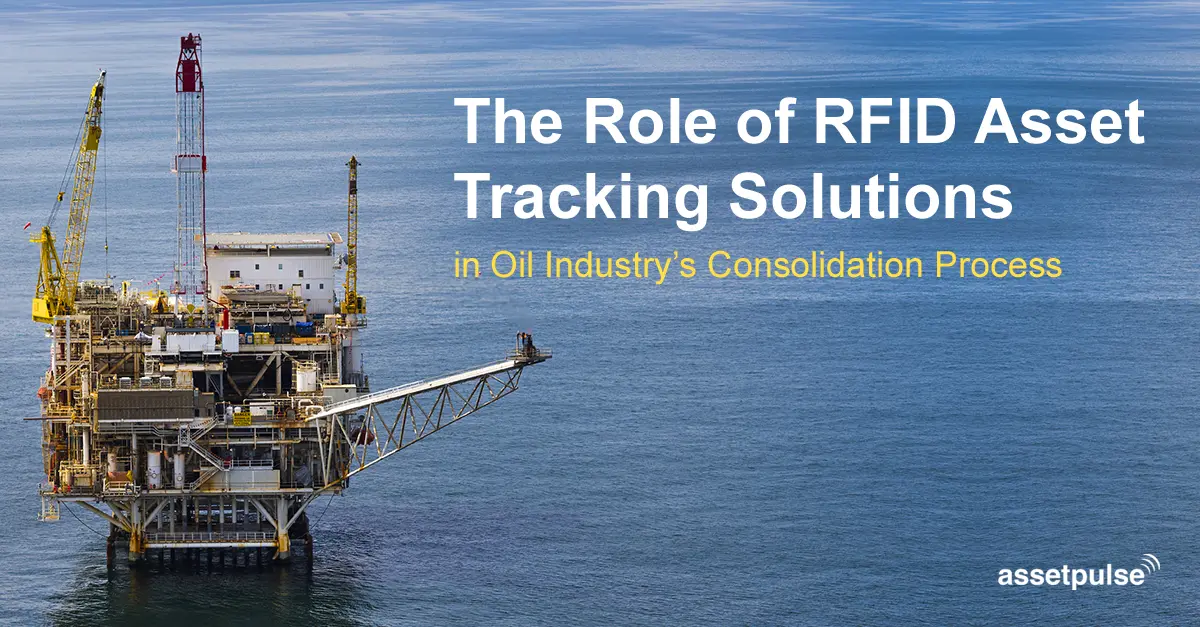
The Role of RFID Asset Tracking Solutions in Oil Industry’s Consolidation Process
As the world oil markets continue to be in flux, consolidation within the oil and gas industry, especially in North America, is accelerating. The small to medium business sector is seeing significant activity. Companies are being acquired, not only for their customer base, but also for their assets. Organizations that are positioning themselves as acquisition candidates need to streamline their business processes and show enhanced visibility of their assets. This makes them more attractive to prospective acquirers. RFID Asset Tracking…