In the competitive landscape of medical device manufacturing, precise asset management is crucial. One prominent manufacturer encountered recurring challenges in tracking essential laboratory equipment and other assets. Conventional manual methods not only consumed valuable time but also disrupted core operations. Critical equipment —ranging from high-precision microscopes to specialized instruments—required constant supervision, particularly in sensitive cleanroom environments. Furthermore, assets stored in cabinets added further complexity. This reliance on manual tracking was increasingly viewed as inefficient and unsustainable. Ready for medical device…
Category: Manufacturing
Explore how asset tracking solutions enhance manufacturing efficiency, reduce downtime, and improve inventory management. Learn best practices for streamlined operations.
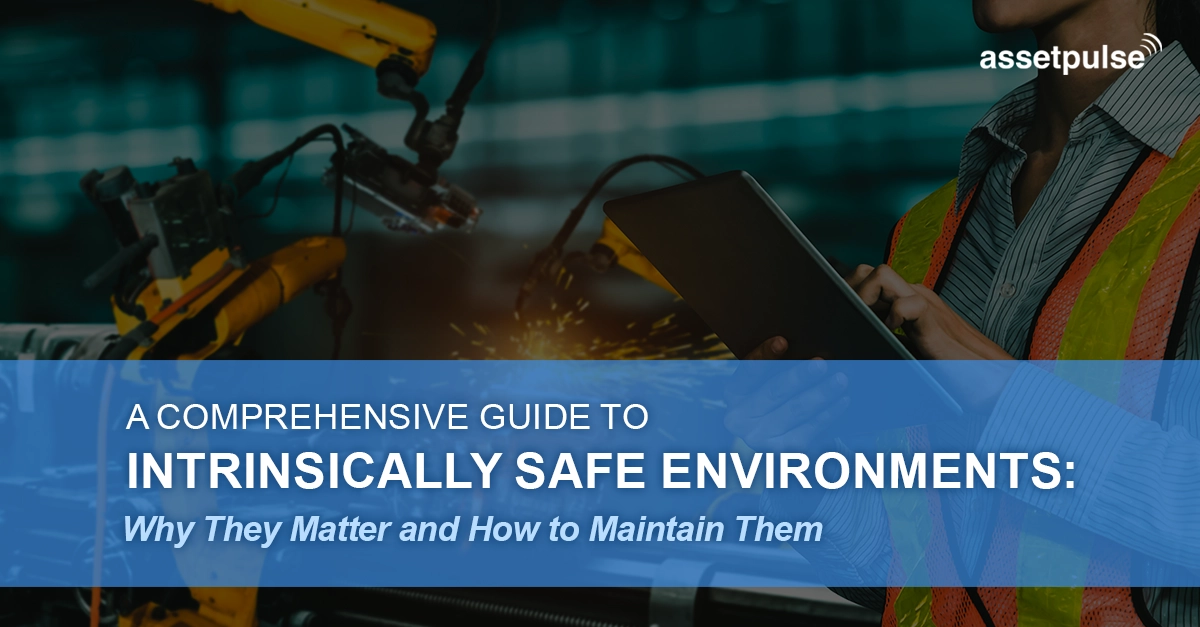
A Comprehensive Guide to Intrinsically Safe Environments: Why They Matter and How to Maintain Them
Industries like oil and gas, pharmaceuticals, mining, and chemical processing operate in hazardous environments that demand stringent safety measures. These settings often contain flammable gases, vapors, or combustible dust, making conventional operations risky. This is where intrinsically safe environments become critical. But what exactly are they? and why are they so essential? Let’s explore. What is an Intrinsically Safe Environment? An intrinsically safe environment minimizes the risk of explosions by limiting electrical and thermal energy to levels that cannot ignite…
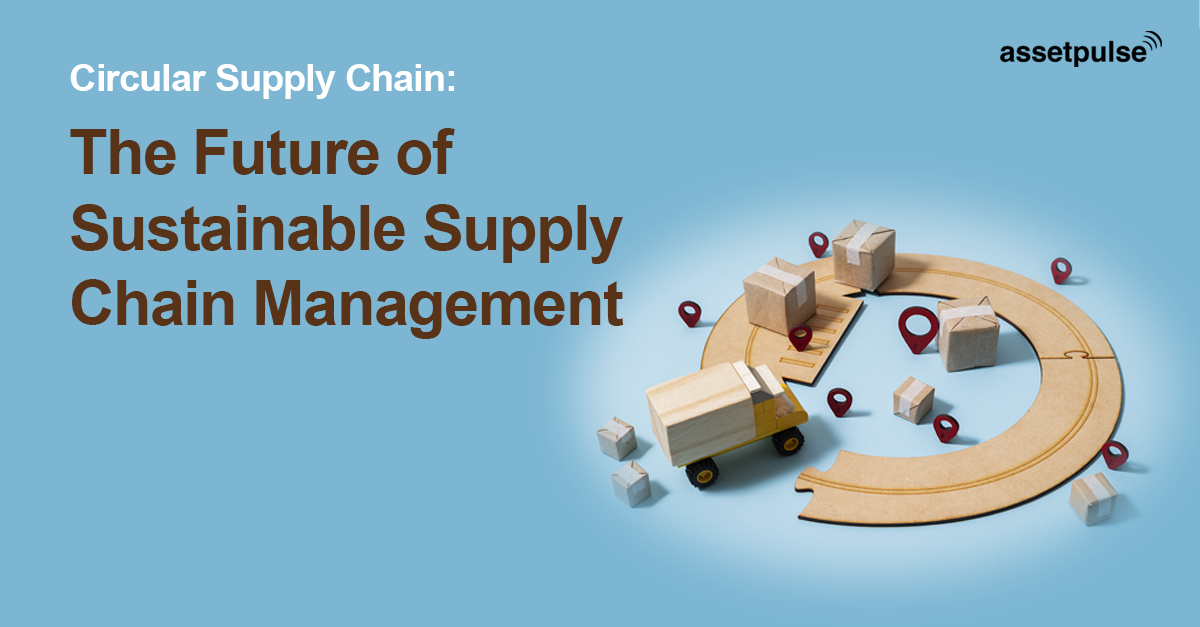
Circular Supply Chain: The Future of Sustainable Supply Chain Management
In a world where resources are becoming increasingly scarce, businesses are searching for more sustainable and efficient ways to manage their supply chains. One transformative approach that is gaining traction is the circular supply chain. Unlike the traditional linear model, where materials are used once and discarded, a circular supply chain emphasizes the continuous reuse, recycling, and refurbishing of resources, significantly reducing waste and environmental impact. But how exactly does a circular supply chain function, and why is it essential…
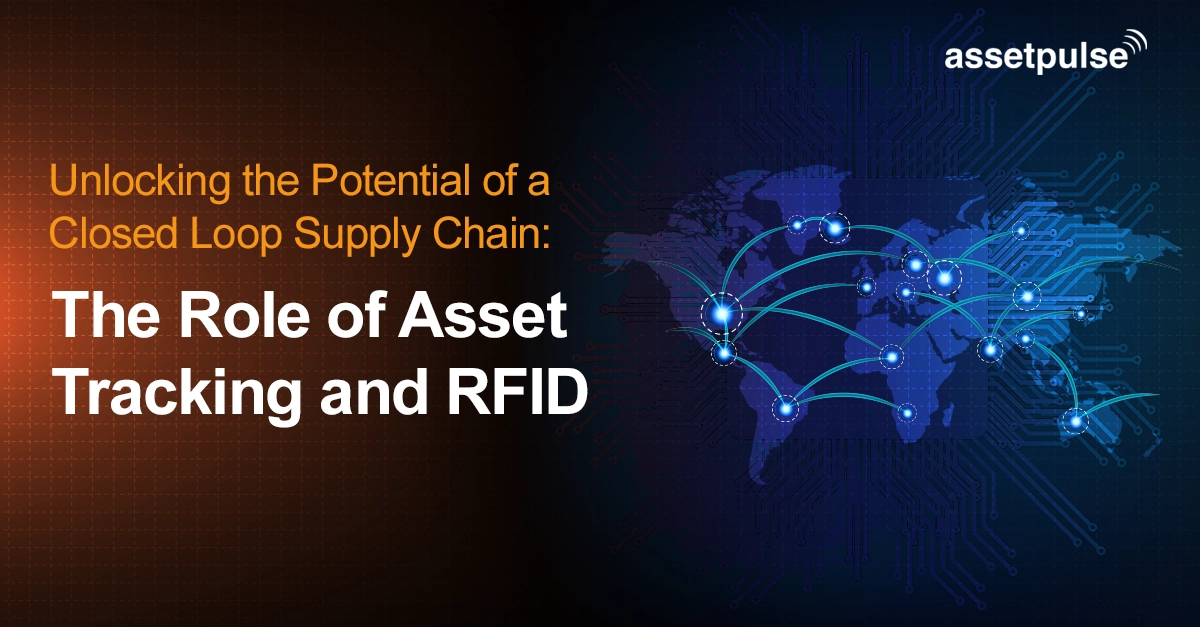
Unlocking the Potential of a Closed Loop Supply Chain: The Role of Asset Tracking and RFID
In an era focused on sustainability and efficiency, supply chains are evolving. One of the most transformative models is the closed loop supply chain (CLSC). It represents a shift from the traditional “take, make, dispose” approach to one that prioritizes reuse, recycling, and sustainability. But with this transformation comes the challenge of asset tracking, a key component that determines the success of CLSCs. Let’s explore the significance of the closed loop supply chain, how it differs from the traditional supply chain, and…
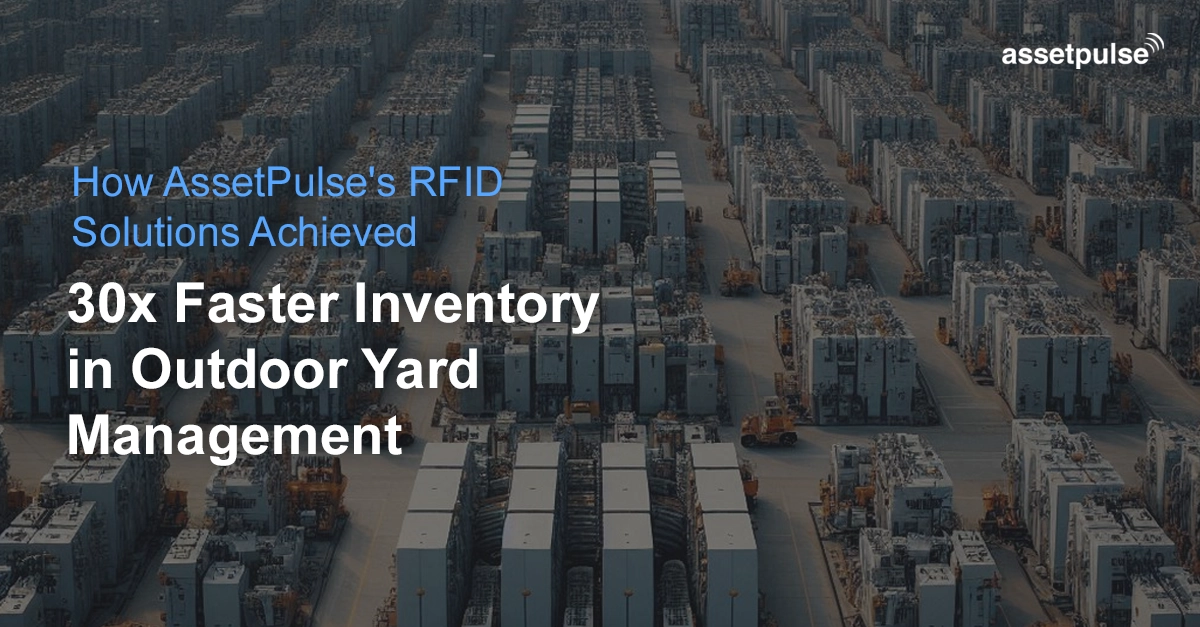
How AssetPulse’s RFID Solutions Achieved 30x Faster Inventory in Outdoor Yard Management
Imagine managing a vast outdoor yard filled with hundreds, even thousands, of assets. Keeping track of this inventory is crucial, especially when it comes to performing inventory on a regular basis. This blog post explores the challenges faced by one of our customers and how they achieved a remarkable 30x improvement in outdoor yard management through AssetPulse’s RFID Solutions tailormade for outdoor asset tracking. The Challenge: Manual Inventory – Time-Consuming and Error-Prone The company, with their extensive yard housing a…