Managing federally funded lab equipment under 2 CFR Part 200 (“Uniform Guidance”) can feel overwhelming. Missed audits, lost instruments, or out-of-date records risk funding, trigger repayments, and damage your reputation. Fortunately, an RFID asset tracking solution from AssetPulse automates every step, without complexity or heavy costs. Ready to streamline 2 CFR Part 200 compliance and safeguard your grants? Check out AssetPulse Low-Cost RFID Asset Tracking Solutions Today! Get Free Consultation Why Equipment Tracking Matters Federal grants often fund expensive lab…
Category: Lab Equipment
Discover how lab equipment tracking improves efficiency, ensures compliance, and reduces losses. Learn best practices for managing laboratory assets effectively.
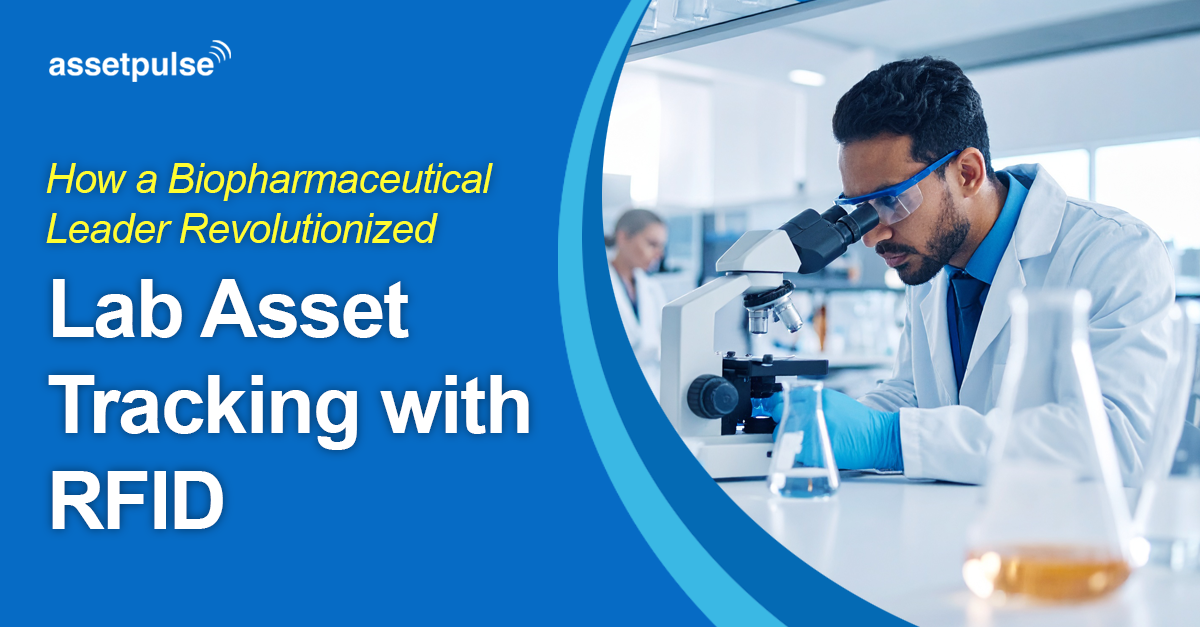
How a Biopharmaceutical Leader Revolutionized Lab Asset Tracking with RFID
Picture this: a global biopharmaceutical company, pushing the boundaries of healthcare with innovative therapies in immunology, oncology, neuroscience, and eye care. Their mission is to transform lives through cutting-edge research and patient-centric solutions. But behind their groundbreaking work, a hidden challenge was slowing them down—tracking lab equipment across sprawling facilities. If you’re a lab manager, equipment manager, or inventory manager, you’ve likely felt this pain too. Let’s explore and see how they turned chaos into control with a game-changing equipment…
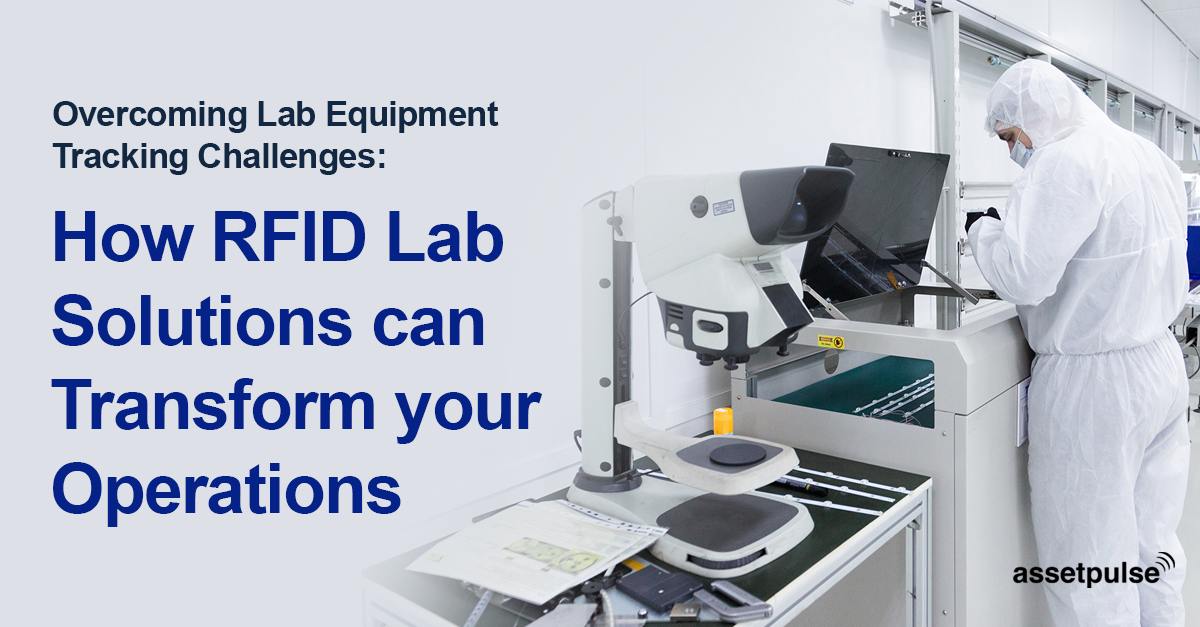
Overcoming Lab Equipment Tracking Challenges: How RFID Lab Solutions can Transform your Operations
Tracking lab equipment is essential for keeping modern labs running smoothly. However, lab equipment tracking continues to be a significant challenge, with traditional methods often falling short. From manual tracking systems to barcodes, these outdated approaches are prone to errors, inefficiencies, and wasted time. As labs continue to evolve, the need for smarter and more efficient lab solutions becomes apparent. RFID technology is a game-changer that promises to revolutionize lab equipment tracking and management. Looking to streamline your lab’s operations?…
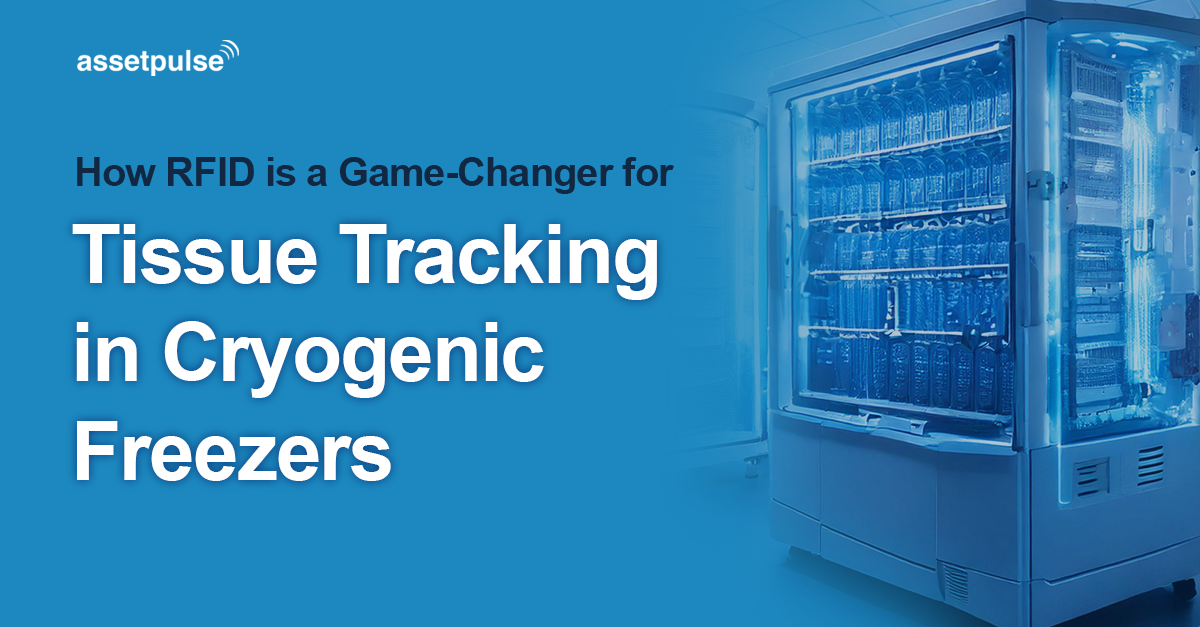
How RFID is a Game-Changer for Tissue Tracking in Cryogenic Freezers
In laboratories, where human tissue samples are critical to groundbreaking research, managing and tracking these samples accurately is essential—especially when they are stored in cryogenic freezers. RFID is changing the game by enabling efficient, precise and reliable tissue tracking, which can dramatically reduce manual effort, risk of contamination, and compliance concerns. RFID, with its wireless tracking capability, eliminates the need for direct line-of-sight scanning, enabling labs to keep accurate records of samples in real time, even in sub-zero environments. This…
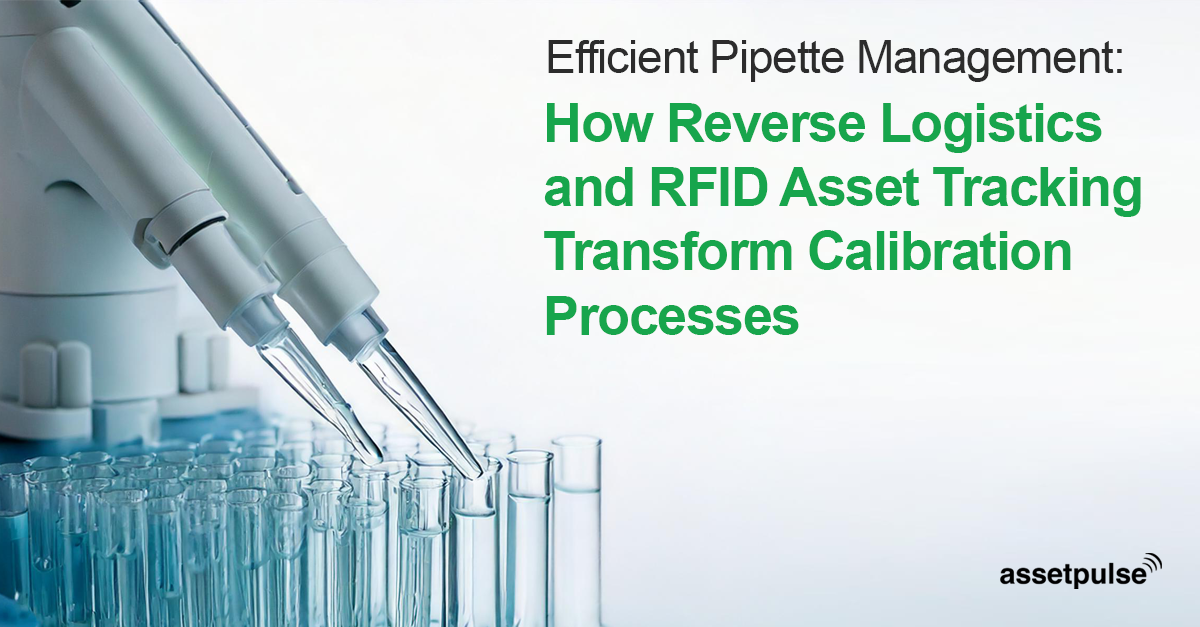
Efficient Pipette Management: How Reverse Logistics and RFID Asset Tracking Transform Calibration Processes
In laboratory settings, accurate and reliable equipment is essential for achieving precise results. Pipettes, one of the most frequently used tools in labs, need regular calibration to maintain their accuracy. However, managing pipettes and ensuring they are calibrated correctly can be a complex task, especially when they need to be sent back to manufacturers for recalibration. Reverse logistics is crucial in tracking pipettes during this process, and RFID asset tracking has emerged as a smarter, more efficient way to manage…