Quick Summary: Why RFID for Inventory Management? The Case for RFID Tags in a Modern Business In today’s data-driven world, relying on manual inventory tracking can lead to blind spots and labor-intensive processes. RFID (Radio Frequency Identification) technology offers a streamlined alternative, giving enterprise organizations real-time insights into their assets, tools, and equipment. By adopting RFID tags for inventory, you can drastically reduce errors, minimize loss, and enable proactive decision-making across the entire operation. RFID Tags for Seamless Inventory Management! AssetPulse RFID Solutions…
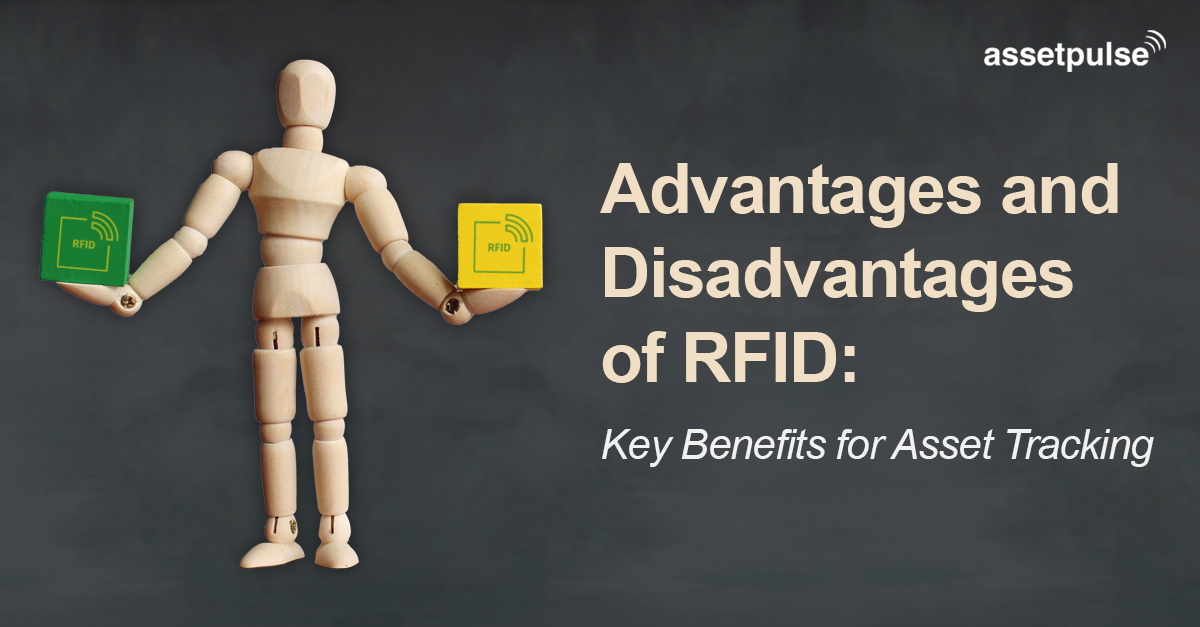
Advantages and Disadvantages of RFID: Key Benefits for Asset Tracking
If you’re evaluating RFID to replace or supplement barcodes, you’re likely asking: “What are the advantages and disadvantages of RFID?” and “Why is RFID important?” Radio Frequency Identification (RFID) has been around for decades, but recent innovation shave made it more reliable and cost-effective. Today, RFID tags and scanners help businesses in manufacturing, healthcare, IT, Labs, and many other sectors. Below, we’ll explore the key benefits (advantages) of RFID, as well as some drawbacks you should consider before deploying an RFID tracking system. Want to…
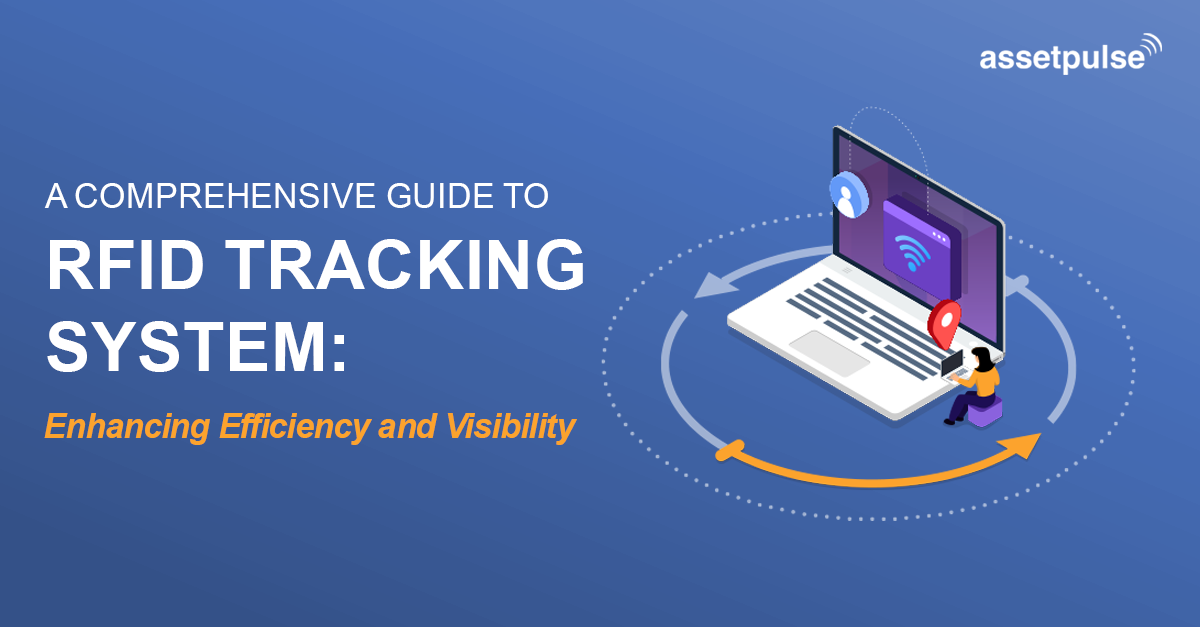
The Comprehensive Guide to RFID Tracking System: Enhancing Efficiency and Visibility
In today’s dynamic business environment, having precise control over your assets isn’t just a luxury—it’s a necessity. For enterprises looking to streamline their operations, an RFID tracking system offers a proven solution. This guide will walk you through what RFID tracking system is all about, its key components, and show you how this technology can transform your operations by boosting accuracy, cutting costs, and improving overall efficiency. Want to know how RFID streamlines your operations? Discover the power of AssetPulse…
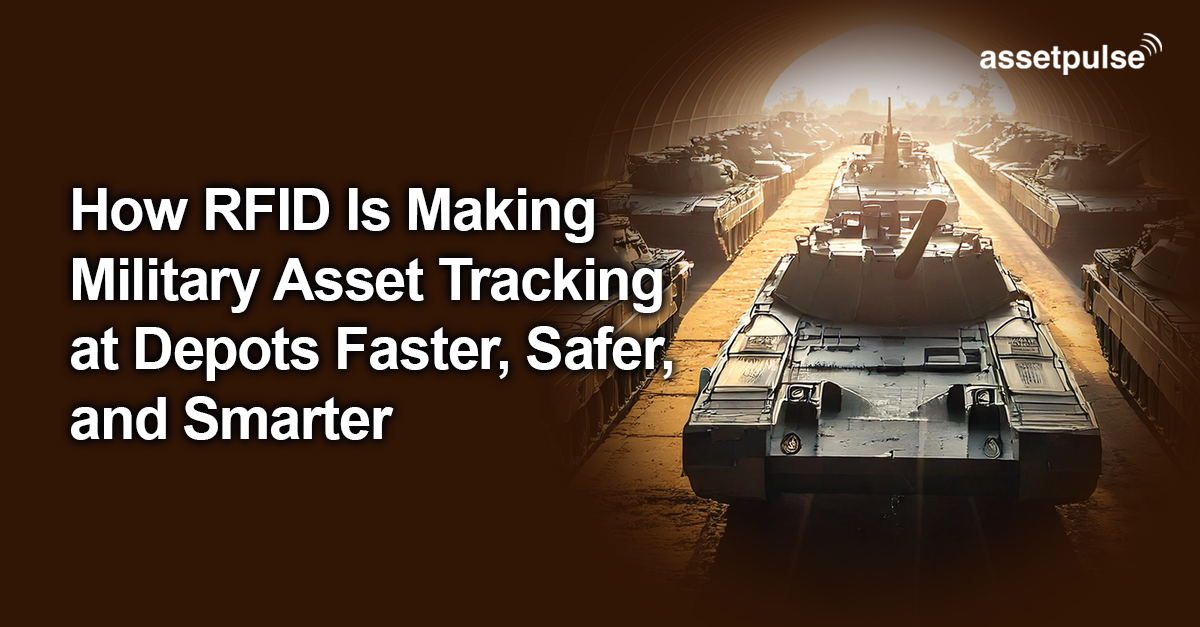
How RFID Is Making Military Asset Tracking at Depots Faster, Safer, and Smarter
Managing a massive army depot—packed with thousands of tanks, trucks, and weapons—is a huge challenge. Old-school tracking methods, like writing down serial numbers by hand or using paper logs, are extremely inefficient, messy, and error prone. These outdated asset tracking systems can’t keep up with the speed of modern warfare. That’s where RFID (Radio Frequency Identification) comes in handy. This post breaks down how RFID fixes these problems and why it’s a game-changer for modern military facilities. Upgrade your depot with RFID…
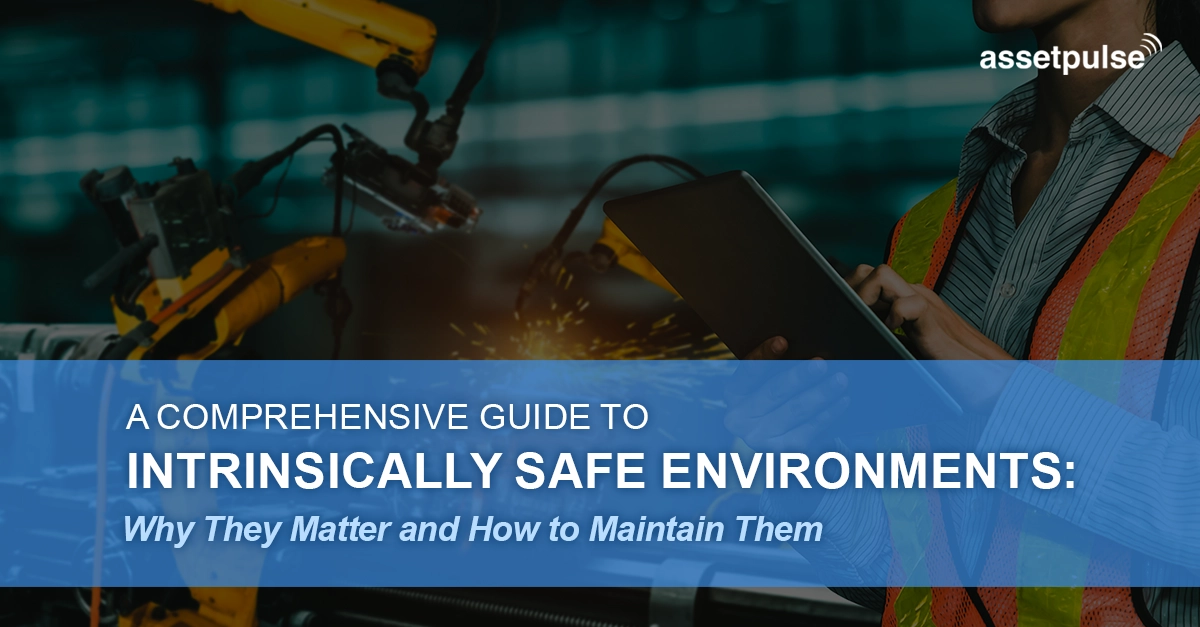
A Comprehensive Guide to Intrinsically Safe Environments: Why They Matter and How to Maintain Them
Industries like oil and gas, pharmaceuticals, mining, and chemical processing operate in hazardous environments that demand stringent safety measures. These settings often contain flammable gases, vapors, or combustible dust, making conventional operations risky. This is where intrinsically safe environments become critical. But what exactly are they? and why are they so essential? Let’s explore. What is an Intrinsically Safe Environment? An intrinsically safe environment minimizes the risk of explosions by limiting electrical and thermal energy to levels that cannot ignite…